椙山女学園大学 現代マネジメント学部教授 澤田善次郎氏
前回のスペシャリストから、医療質安全学会が必要だというお話をいただいたが、学会の立ち上げにはどういうノウハウが必要なのだろうか。それを探るべく、今回のスペシャリストには、日本生産管理学会の実質的な創設者であり、現在同会の副会長である澤田善次郎氏にご登場願った。椙山女学園大学の現代マネジメント学部教授でもある氏に、学会の活動内容、医療界への提言などを伺った。(取材日;平成16年10月29日)
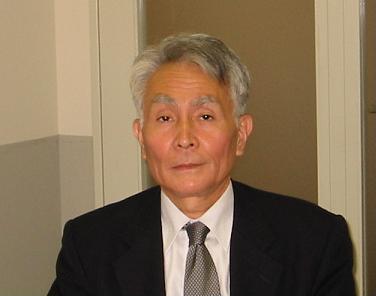
1.学会の活動内容
-今年創立10周年を迎えた「日本生産管理学会」の活動について教えて下さい。
(理論化・普遍化)
「実践経営研究会」として約5年間の研究活動を経て、平成6年4月に「日本生産管理学会」が創立されました。基本的な考え方は「理論と実践の融合」です。会員の構成は、学者の方50%、実務の方50%、という割合でずっときています。
活動としては年に2回開催される全国大会がメインです。全国は6支部に分かれ、それぞれにテーマ別研究会があり、活発な研究活動を行なっています。特に中部支部には、さらに小さい30位のQCサークルのようなものがあります。また、本学会独特のこととしては、「工場管理」「ISOマネジメント」という月刊誌(発行:日刊工業新聞)に毎月記事や各々年2回程特集号(1回は50ページ、1回は150ページ程度)を書かせてもらっています。この担当ページの作成を目標に、会員は単に研究するだけではなく、それをまとめて発表するということもしながら、研鑽を続けています。
日本の生産管理は、実践は進んでいるけれど、理論化が十分ではありませんでした。学会としては、進んだ実践を理論化してそれを一般に伝える普遍化が大きな役割だと考えています。以上のような活動の成果としては、専門家向けの『理論と実践シリーズ15冊』『生産管理ハンドブック』などにまとめあげ日刊工業新聞社より出版しています。
(社会への働きかけ)
今モノづくりの現場で問題なのは、技術・技能を伝承出来る人がだんだん少なくなっていることです。技術・技能は人に帰属しています。大きな世間を騒がすトラブルは、リストラで人を一気に抜いてしまった時に多く起きています。そこで、学会として、判り易い実務書や現場の管理監督者向けの教材も作成し、出版や「通信教育」を実施したり「ビデオ教材」を作り、生産管理の普遍的な知識・技術・技能などを普及しています。
このような本などの発表物を出すということになると、何度も集まらなければなりません。実践に携わっている人には時間がない場合には、定年退社した方々に協力してもらうこともあります。とにかく何度も集まって検討して本などの形にしていきます。大体1年に4~5冊程世に出せるよう出版社などに企画・提案をしています。企画物にははっきりした目標がありますから、誰にどこをやってもらうかも自ずと決まってきます。明確な目標がないと日常活動を粘り強く、展開することは難しいでしょう。
さらに、日本規格協会などの機関でそれらを活用した講習会・講演会を開催して普及に努めています。
例えば、「目で見る工場診断」(編集:名古屋QS研究会 出版:日本規格協会)では、読者が自己採点して工場診断した後の、改善のポイントや進め方なども記述しています。
つまり、それらを活用し国内だけでなく海外の技術指導のテキストとしても活用されています。ただ研究活動をしているだけではなく、ある程度社会に働きかけ、受け入れてもらい、その反応をみながら活動を推進しています。
(今後の課題)
●国際化
本学会は今まで国際的な交流をあまりしてきませんでしたが、最近はイギリスの専門雑誌の特集号を全部任せてもらうなど、国際的な活動を行ない始めています。
現在は、2008年開催予定の第3回生産管理国際学会の日本での開催(第2回大会はメキシコのカンクーンで513名の参加を得て開催された。参加国数は38ヶ国)が学会としての大きなターゲットになっています。目標を決めてそれに向かって研究活動に取組んでいます。
生産管理については、日本の学者が提唱して普及したタグチメソッド(注1) という手法もありますが、基本は欧米から習ったものが多いのです。つまり、進んだ実践を理論化し、世界に紹介することを怠ってきました。
例えば、アメリカの経営管理の始まりであるIE(Industrial Engineering=経営に直結する全社的な製造技術)を学んで、MIE(儲けるIE)を作ったのが「必要な物を必要な時必要なだけ造る」というトヨタの生産システムJIT(ジット、Just In Time)です。
日本の製造業は米国のSQC(統計的品質管理)を導入し、日本型TQC(全社的品質管理)を作り、今はTQM(全社的品質経営)の時代になりました。日本のモノづくりは大量生産、大量消費で利益をあげればよいとしてきましたが、環境管理についてもっと事前に理論化・普遍化の努力をすべきでした。日本が不十分なことは諸外国から学ぶべきです。謙虚に学び努力した結果、現在では環境管理面でも日本は世界のリーダー役を果せるようになっています。
とはいえ、原理原則に変わりはありません。日本もアメリカも欧州も、良い企業ではどこも「人を大切にし、技術を大切にし、消費者・生活者を大切にする」ということで発展しています。
●研究者の養成
経営学の中で生産管理を扱っている学者は少数でしたし、まだ多くはありません。生産管理関係の学者を養成したくても、親となる人がいなければ、子や孫が育ちません。新しい研究者を今までのように多く安定的に雇える大学もだんだんと少なくなってきています。現在、大学の30%は定員割れの状況です。また、大学には、組織的に教育内容や授業方法などを研究し、教員に対して研修すること(FD=Faculty Development)が求められています。
そこで、学会として、若い研究者・教育者を養成することや教材開発などをしてもらうことも課題と考えています。例えば、学会の附属研究所のようなものを創り、就職が決まらない若い研究者・教育者に、附属研究所に一時期所属してもらい、教材開発などをしながら学問の世界に飛び立つ準備をしてもらうことができればと思っています。そういうことも考えていかなければいけない時代になっているのではないでしょうか。
●第1次・第3次産業への働きかけ
第1次、第3次産業に対して生産管理の考えを役立てることも課題と考えています。新しい商品・サービスをどのように作り出していくかは、製造業だけでなく他産業でも取り組んでいます。例えば、農業の生産管理、ソフトウェアの品質管理・原価管理、病院の品質管理・原価管理・安全環境管理など、新しい側面へも広げていかなければいけないと思っています。
2.トヨタの強さ
-では、第3次産業である医療界に、参考になると思われる生産管理の考え方を説明して下さい。
(自働化)
生産管理の目的は「良い商品やサービスを安く、納期通りに、必要数、生産期間を短く、在庫量少なく、安全で、環境にも配慮して、皆がやる気になって提供していく」ことです。これが、長期的、短期的な企業の利益につながります。
例えば、これからの作業の管理は「ハードウェア」「ソフトウェア」「ヒューマンウェア」という3つの側面から考え実施すべきです。この3つの側面の充実で作業の改善と標準化を進め、「前工程より不良品を受取らない」「自工程が不良品を作らない」「後工程に不良品を流さない」という仕組みを上手に作ったのがトヨタ自動車です。
ハードウェア面では、自働化とポカヨケという2つの柱が重要です。トヨタでは不良品を作り続けることが無いようにするシステムを、ニンベンのついた自動化(=自働化)と言っています。不良品でもどんどん作るのは単に動いているだけで働いていることにはなりません。また、「ポカヨケ」とは、誰がやっても間違いがない仕事ができるようにする、もし間違ったときには仕事が進行しないようにしたり発見できるように物理的にする「工夫」です。
ソフトウェア面は、作業標準(マニュアル)と目で見る管理(異常か正常か誰でも判るようにすること)という2本柱を充実することです。
ヒューマンウェア面は、技量や技能の向上と良いもの、安いもの・・・を作ろうという意識を高めることが2本柱です。
これら3つの側面と6つの柱をしっかり確立して強い生産システムつまり、生産した商品数100万個の中に1個の不良の発生や流出を許さないという強いシステムを作っています。特に大事なのが「自働化」「ポカヨケ」の考え方とその「工夫」です。ここがしっかりしないまま仕事のシステムを作ってはいけません。医療面でも応用していただければと思います。
(源流管理)
トヨタは、『標準作業票など』の独自の作業管理の帳票類を創り・活用し、品質、原価、納期、量、安全、環境を一元的に源流管理しています。源流管理とは、製品の企画段階や開発・設計・生産準備段階において製品の品質や他の目標に係る問題を未然に発見し解決していくことです。発生した問題だけをもぐらたたきのように解決するのではなく、問題が発生する前に対策をとることです。源流管理をしっかりやることで経営の勝負の70~80%がつきます。トヨタはこうした予防、未然、事前の管理が優れています。
また、ただ標準だけ作っても意味がありません。目的・目標が果せるように事前に改善や改革(大改善)をして、標準を作って維持するというのがトヨタの考え方です。それが管理(マネジメント)です。つまり、よい管理者とは問題を未然に察知し解決する人です。
(モノづくりは人づくり)
トヨタは、協力企業に対しても、ただ原価を下げなさいというのではなく、協力企業と一緒になって改善出来る人を派遣し実践的に教育し人を育てながら改善を促進しています。そして、無駄を省いて原価が下がった成果は、努力した協力企業とトヨタと消費者に3等分し配分されます。
トヨタは「モノづくりは人づくり」と考えます。社内で教材開発や先生の養成をし、社員を教育するということもしています。協豊会と呼ばれる協力企業(部品メーカー149社)の組織(協力会)でもSQC(統計的品質管理)を学ぶ講座を開催し、実践的教育を自主的に実施するよう指導しています。何も難しいことをやっているわけではありません。当然やるべきことを関係する人達全員で実施し、日々改善を続ける。そういうことの繰り返しがトヨタの強さだと思います。
(先を読み、利益を確保する)
中国の作業者賃金は日本の1/20~1/25です。中国と同じ事をやっていたのでは日本の仕事はなくなってしまいます。中国の20~25倍の賃金を得続けようとするなら、新しいサービスや商品を開発して、お客様に応えていくことが大事です。
生産管理の基本は、品質・原価・納期・量の管理であり、それに安全衛生・環境・作業・設備・資材・情報の管理が含まれます。しかし、ただ今迄の生産管理だけを考えていたのではダメです。経営の一環としての生産管理、つまりもっと広い概念で「生産管理」を考えていかなければなりません。 我々が新しく追究しなければならないのは、先を読むことです。そうすれば中国にも勝てます。例えば"プリウス"のような環境にやさしい商品、燃費効率が高い商品を開発・製造すれば、競争に勝てます。
原価管理(コストマネジメント)ということが言われ出したのは昭和40年代初め頃ですが、トヨタはその頃すでに、原価企画(コストプランニング)と言っていました。原価企画とは、新しい商品を作るときに、売値をこれだけにしたい、カローラはこの値段だったら一般大衆が買ってくれるだろう、この値段でやって利益をこれだけ上げるには許容原価はこれだけになる、これだけのつまり許容された原価で設計・製造しなければならない。そのようにコストプランニングして設計・生産準備して作り方を決めていくことが大切です。
(顧客感動)
これからは原価の時代から価値の時代(ブランドの時代)になっていくと思います。価値というのは顧客満足(Customer Satisfaction)を得ることとも置き換えることができます。トヨタは平成9年から顧客感動(Customer Delight)運動を展開しています。商品やサービスに新しい付加価値をつけることで、顧客に応えています。プリウスのようなハイブリッド車にすれば当然価格は上がりますが原価も高くなります。そのため一方では、原価低減を強力に行なっています。
また、これからは、商品のライフ・サイクルを通して発生するコストを全体的に管理しようとするライフ・サイクル・コスト・マネジメントが要求されています。車の場合、消費者は故障しやすいとか、燃費効率が悪いとかいうことも購買時に考慮するようになるでしょう。さらに、生活者としての私達は排気ガスを多く出すような車には(社会的)ペナルティを課すべきです。
3.医療界への提言
-製造業にはトヨタ自動車というリーダー的存在がありますが、医療界でのそういう存在はまだまだ模索中と思われます。現代マネジメント学部教授としての視点からも、医療界へアドバイスをお願いします。
(表彰制度)
Best Practice (最優良の実践例)を実施した企業に与えられるデミング賞(注2) 、マルコム・ボルドリッジ賞 (注3)などのような表彰制度が大切だと思います。悪いことばかりではなく、いいところを見つけて褒めて評価、表彰していくことです。長所を伸ばすようなやり方です。昔は「悪いところを直せ」とはっきり言っても耐えられる人が多かったのですが、最近はコーチングなどの考え方が一般的になり、ある程度ほめて育てるという側面も大事になってきています。
(守・破・離、そして自主経営)
私は大学の「現代マネジメント学部」で、自分、家庭、職場、会社、ひいては地域や国や国際機関、非営利組織などのマネジメントを研究・教育しています。
自分の仕事の目的・目標をしっかりつかむ。それが果たせるように事前に自分の仕事を改善して、作業標準を作る。その後、作業標準を体が覚えこむまで訓練する。それを決めたとおりに行なったか、目的・目標が果たされたかを自分でチェックし、自分で直していく。こうした「自主管理」をすることを通して、小さい管理のサイクルを自分で繰り返して回していくことが大切です。
何かを学び、ひとり立ちしていくまでには「守・破・離」の順に段階を進んでいくと言われます。「守」は、まず教えてもらって忠実に守っていくという段階。「破」はそれを打ち破っていく段階、「離」はそれを離れて自由にやっても原則に従ってやれる段階です。
人に命令されたから決められたように仕事をするのではなく、最終的には自分の仕事の管理や経営(セルフマネジメント)が自分自身でできるようにまでなることです。1人ひとりが高い志を持ち、問題を事前に見つけ事前に解決する、そういう意識を強く持ち、毎日を全力で生き抜くことが大事です。
(現実を正しく伝える)
医師やコメディカルの閉鎖された世界は、社会ともっと交流すると変わるのではないでしょうか。その時間的・精神的余裕がないのが良くない点です。医療に関わっている人は使命感を持たれているし、優れているし、努力していると思います。それをいかに正しく伝えるか。企業のIR (注4)のようなものが必要なのではないでしょうか。こういう良いこと、努力をしているということを、もっと患者や社会に伝えた方がいいと思います。献身的に一生懸命やっている姿が正確に伝わっていないと思います。正しく理解してもらわないと、皆消耗してしまいます。皆で告発合戦のようなことをやっても何の意味もありません。医師もコメディカルも人間ですから休ませなければいけないし、勉強もさせなければなりません。また、正しく評価、表彰(賃金だけでなく賞賛すること)されなければなりません。現場で、知識と技能の棚卸とその評価を個人別に実施して全員に専門家として必要な知識や技能(技術)を計画的に身につけてもらうように教育・訓練することが必要です。医師やコメディカルにその時間と資金を与える必要があります。
患者の甘えの部分とそうでない部分も、もっとはっきりさせたら良いと思います。不健康な生活習慣や限度を超えた治療などをしていれば医療費が高くなるのは当然です。これからは予防や前向きな医療にもっとウェイトを持っていった方が良いでしょう。
(患者の要望・欲求に個別に応える質の高いサービスを)
終戦後は、「物不足」でしたから生産者中心でした。だんだんそれが解消され現在では、「物余り」状態になり消費者中心になっています。物不足の時代は、標準化された商品を大量に生産・販売していたが、現在では各企業は多品種少量生産(変品種変量生産)でお客様の要望・欲求をビフォアサービス・アフターサービスも含め満たそうと努力しています。生命や健康より大切なものは無い訳ですから、質の高い(安全は当然)医療に見合うお金を支払っても良いと思う患者も多いと考えます。顧客である患者の(個別の)要望・欲求を満たすメニュー、サービスをそれに見合う価格で開発・提供することも求められています。
また、顧客の満足は従業員の満足があってはじめて可能ですし、一方では社会の満足も前提としてあることを忘れてはなりません。もっと自由に発想し、真の顧客満足・顧客感動が得られるように関係する方々全員で努力されることが必要な時代ではないでしょうか。
(用語解説)
- (注1)タグチメソッド
- 品質工学と呼ばれる、田口玄一博士が開発した開発・設計段階で適用される工学手法。はじめにバラツキを減らすことを優先し、次に目標値にあわせこむという2段階設計法をとる。
- (注2)デミング賞
- 企業から独立した第三者(デミング賞委員会)が、企業の製品品質管理の仕組みを評価し、効果的な品質マネジメントを行なっている企業を表彰する制度。
- (注3)マルコム・ボルドリッジ賞
- 1987年レーガン政権の下、米国の国家的競争力の工場を目的とし、設立されたもの。創造的でかつ継続的に顧客が満足するクオリティ改善、その実施度合いの評価、その改善領域発見のための優れた経営システムを有する企業に与えられる賞。
- (注4)IR
- 「Investor Relations」の略語。企業が投資家に対して、その企業の戦略や財務状況、研究開発状況などを正確に伝える広報活動のこと。
(参考図書)
![]() |
「トヨタ生産方式で品質管理を徹底するためのキーワード集」
|
日本生産管理学会は、その前身となる研究会としての活動が5年ぐらいあったという。設立2年半の本ネットワークには、まだまだ活動内容を熟考する余地があると感じた。
ただ、「人を大切にし、技術を大切にし、消費者・生活者を大切にする」という原理原則は、医療界にも通じることだと思う。技術、消費者(=患者)を大切にすることはもちろん、従事者を大切にし、教育していかなければならない。トヨタが言う「モノづくりは人づくり」を、「医療安全は人づくり」と捉えてみてはどうだろうか。